✉️ [email protected] | 📞 +971-4-2675252
Home / Applications / Abrasive Blasting
Abrasive Blasting
Al Khamis Equipment LLC sells products designed for sand blasting. Read more about our products for abrasive blasting.
Abrasive Blasting
What is Abrasive Blasting
Abrasive blasting or sand blasting is the process of applying an external abrasive material at high pressure (such as sand, air, or water) to the surface of another material with the intention of changing its surface consistency or as a method of cleaning, preparing or finishing. We generally see sand blasting techniques used for the surface preparational works of metal, glass, stone, and wood within industries such as:
- Ship Building.
- Welding and Metalworking.
- Machining.
- Automotive Body Construction.
- Repair and Maintenance.
- General Construction.
- Painting Works.
- Various Material Maintenance and Deep Cleaning.
- Glass Works.
- Industrial Cleaning.
- Engraving Services.
Abrasive Blasting
How does Abrasive Blasting work?
The basic operational process of sand blasting equipment is fairly similar throughout the variety of different types available for use. Firstly the operator must select a blasting abrasive to best suit the task at hand; as can be seen on the graph below the type of abrasive selected depends upon the desired surface finish, the characteristics of the abrasive itself and the material to be worked upon.
When the abrasive material is selected we then place it into the blasting pot. This pot is a component of the blasting equipment that has been designed to withstand pressure and securely house the abrasive material until it is ready for use. As the operator starts the blasting machine an external pressure (usually in the form of compressed air) is introduced into the blasting pot which forces the abrasive material through an outlet. This outlet is connected to a hose line for the abrasive material to travel along until it reaches the nozzle component of the hose. From here, the abrasive material is allowed to propel rapidly into the surrounding atmosphere and is directed upon the asset. As the abrasive material makes contact with the surface of the asset, the combination velocity and provoked irritation (of the abrasive material) remove small amounts of the surface material until the desired finish is achieved.
Vertidrive
Vertidrive Abrasive blasting solutions
The VertiDrive team is the proud designer/supplier of sand blasting robot solutions: the VertiDrive M3 and the Vertidrive M7. Robotic blasting equipment in general has proven to be a massive leap forward for the sand blasting industry. We like to highlight this through the tested comparisons we have made between Robotic Blasting Equipment and Manual Blasting Equipment.
Robotic sand Blasting is:
- 7x more efficient,
- 8x faster than manual methods,
- 86% reduction in costs.
The M3 and M7 have been designed with much consideration for maximum productivity with lower operational costs. These unique solutions act as carrying platforms for traditional hand-held blasting equipment, an operator simply needs to connect the robot to the hose line of a hand-held blaster and they are ready to blast. The M3 and M7 will then convert the single hose line of this hand-held system into 3 separate blasting nozzles which spread the blasting abrasive with triple efficiency across the desired surface.
The M3 and M7 are free to move across the face of metallic structures through the usage of permanently attached, powerful magnets. Horizontal, vertical, curvatures, corners, and overhead surfaces are all a breeze for these solutions. On top of this, the robot’s operator will always be based safely on the ground and far away from any health and safety hazards such as working at height or inhalation of microscopic debris.
Benefits
Benefits of Using Vertidrive
- Multi-purpose
- No need for scaffolding or cherry pickers
- Turns the work into a one-man job
- Safe, clean and efficient operations
- Closed systems available
- Low maintenance robots
- User friendly
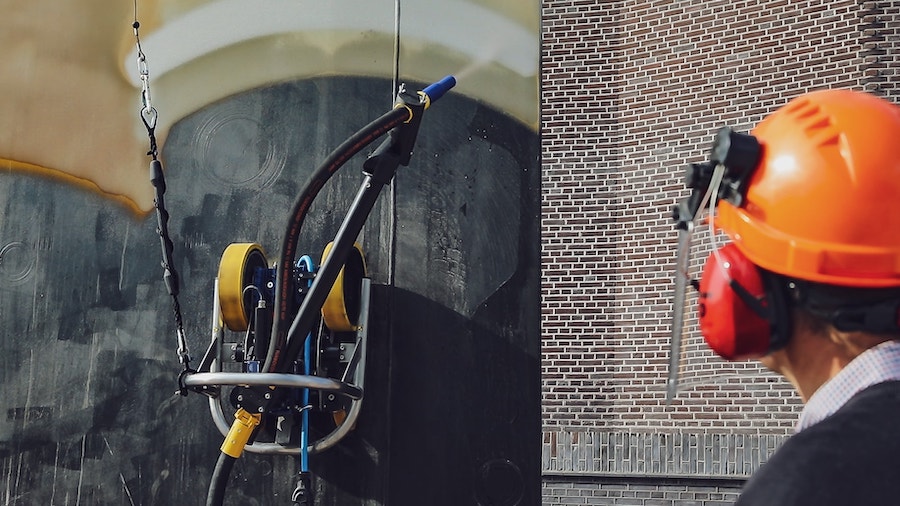


Our Solutions
Vertidrive's Robot
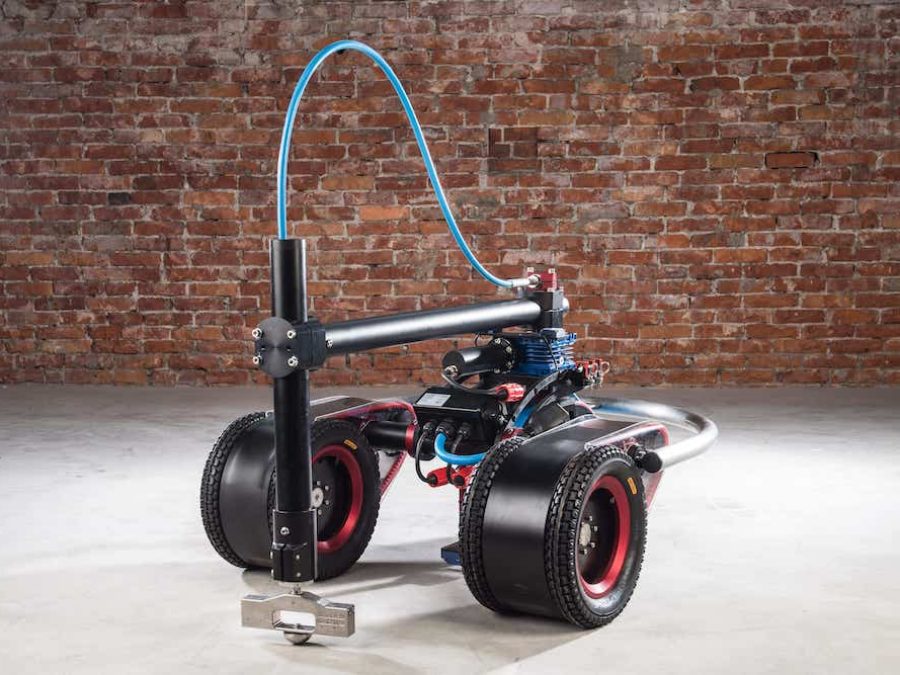
Vertidrive M3
- 60 m2 / 646 ft2 per hour
- 8x faster than manual work
- Horizontal, overhead and vertical surfaces
- Multi-purpose solution
- Interchangeable applications
- 1500 mm(60″) cleaning width
- Remote Controlled
- Controlled to Vertidrive M4
- Versions: Electric, Pneumatic, ATEX Zone II
- Fits through 24″ manhole
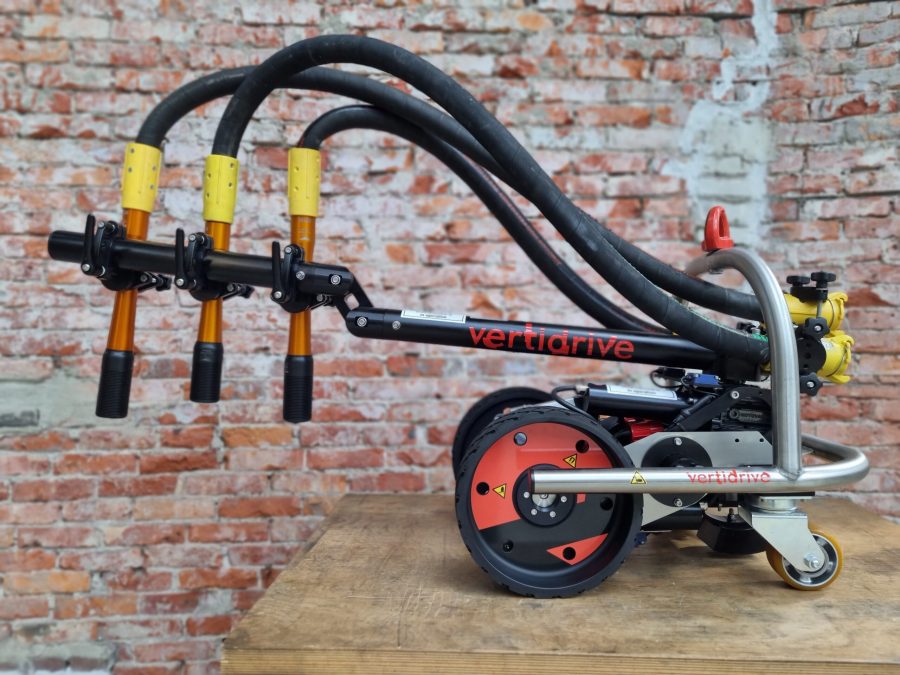
Vertidrive M7
- 60 m2 / 646 ft2 per hour
- 8x faster than manual work
- Horizontal, overhead and vertical surfaces
- Multi-purpose solution
- Interchangeable applications
- Multi-directional swing arm
- 1500mm(60″) cleaning width
- Compact, agile design for smaller working radius
- Wireless control
- Powered by 70Vdc motors